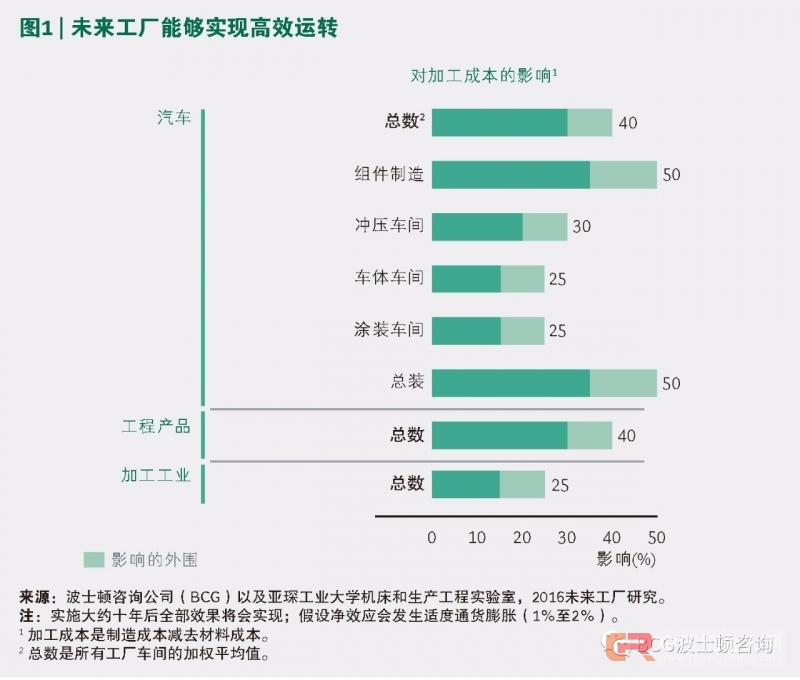
In this report, we mainly studied automotive suppliers and OEMs. In recent decades, such companies have taken the lead in using innovation to increase production efficiency. They took the lead in implementing the future factory elements, which helped to accumulate experience in use, identify opportunities for improvement, and become models for other industrial manufacturers to learn. What is the future factory? The factory of the future is an idea, which means that manufacturers should improve production efficiency by improving the plant structure, plant digitization, and factory processes. We will discuss each element and provide examples of how leading automotive suppliers and OEMs are testing these new concepts. Plant Structure The layout of the future plant structure is more flexible and more oriented, with modular production line installations and sustainable production processes. In our survey, respondents in the automotive industry hope that factory structure will play an important role in future factories. 86% believe that this driving force will become more important in 2030, and 43% think it is very important. Multi-directional layout. In the future, the factory will adopt a multi-directional layout, put the product on the driverless transportation system, and individually guide the production by associating with the production machine. Located at the Audi R8 factory in Heilbronn, Germany, there is no fixed conveyor belt. In contrast, the driverless transportation system moves the body during the assembly process according to the command of the ground laser scanner and radio frequency identification technology. This system can quickly change the assembly layout. Modular production line installation. The future plant structure has replaceable production line modules and production machinery that can be easily reconfigured. At present, Toyota is assembling "simple and neat" production lines at its factories in Mexico and China. The carmaker will use a modular conveyor belt (built on the factory floor instead of a pit) to provide workers with greater flexibility. They can flexibly change the length of the production line and move the wire end equipment. Sustainable production. The purpose of the factory in the future is to achieve ecologically sustainable production, which includes the effective use of energy and materials. Webbast has equipped the plant in Arad, Romania, with LED lighting and an automatic night cooling system, which greatly reduces energy consumption. Factory digitization Manufacturers use digital technology more and more widely. Of the respondents in the automotive industry, 70% said that factory digitalization will become more important in 2030, and 13% think it is very important today. Many companies are introducing more intelligent automated production, using various methods to increase efficiency. Install an intelligent robot. Robots can perform more complex tasks than workers. Robots can also gather information from each product in the process of production and automatically adjust their behavior according to their characteristics. Changan Ford has installed flexible industrial robots on a "white body" welding line. The company plans to use robots and car body skeleton molding systems to process six models on the same welding line and complete conversions for different models within 18 seconds. Use a collaborative robot. Robots can collaborate with workers (without guard fences). In Volkswagen's factory in Wolfsburg, Germany, collaborative robots can help workers tighten hard-to-reach screws. Implement additive manufacturing. Manufacturers have begun to use 3D printing technology to make tools and components. When building the Rolls-Royce Phantom, BMW used 3D printing technology to produce more than 10,000 components, such as central control unit buttons and plastic holders for electronic parking brake systems and sockets. Use augmented reality technology. The use of augmented reality technology - such as wearing smart glasses - enables employees to obtain information within the visual field. This collaborative technology is particularly useful in assembly, maintenance, and logistics. Volkswagen has equipped 3D smart glasses for logistics workers at a German factory for order picking. Application of production simulation technology. Manufacturers are using real-time 3D production simulation technology to optimize production processes and material flow. Using material flow 3D simulation technology, Foglia can respond more flexibly to changes, and operators can also use the visual workflow to adjust the production line. Conduct real training. Using 3D simulations for training helps employees learn in a realistic environment. Using digital models of vehicles and assembly components, Mercedes-Benz has developed a virtual assembly line. Employees can use virtual roles in virtual environments to analyze the best way to accomplish assembly tasks. Decentralized production guidance. Many companies have begun to use advanced technology to communicate between workpieces, machines, and employees to create autonomous production processes. Bosch is developing a tool that can detect their location. Depending on the location of the tool and the information it receives about the exact location of the part, this tool will automatically load the appropriate program and perform certain operations. For example, a screwdriver will adjust its own torque to tighten the screws on a specific workpiece. Conduct big data analysis. Manufacturers are using applications to automatically analyze large amounts of data. At its plant in Lower Turckheim, Germany, Mercedes has used predictive analysis to detect more than 600 quality-influenced parameters to produce a perfect cylinder head. Factory Processes By using new digital technologies, manufacturers have taken lean management to the next level, unleashing its full potential. Our survey results show that optimizing factory processes will become more important in the future. Of the respondents in the automotive industry, 97% said that lean management will become more important in 2030, while 70% said it is now very important. In lean management, two key elements that digital technology can enhance are customer-focused and continuous improvement. Customer-centric. Manufacturers have a deeper understanding of customer needs. For example, through big data analysis, they can obtain feedback from customers' product applications. Instead, companies can use these customer feedback to improve product design and production processes. Many companies also want to be able to use new technologies to understand their customers’ opinions on car production. At Daimler, customers can request modifications at the last minute, such as requesting a color change before the vehicle enters the paint shop. keep improve. Manufacturers are using various new technologies to increase the value of their operations and continuously improve their production processes. The software used by Bosch analyzes real-time production data for fuel injectors. The software monitors process execution rates and identifies operating trends. It can automatically transmit deviation information to operators and correct them. All-In-One Integrated Value Chain In the future, the value chain consisting of suppliers, parts manufacturing, stamping shop, body shop, painting shop, final assembly and customer will realize all-round integration and break the traditional boundaries (see the figure 2). Throughout the entire value chain, the IT system integrates with all necessary production data and will promote production and manufacturing. In a company, this integration can strengthen the links between R&D departments, production departments, sales departments and other functional departments. For example, Continental Tire Co., Ltd. has set up an R&D and production plant to implement all-round integration of all kinds of machinery using various sensing systems and software, thereby accelerating product testing speed. At the same time, this integration can also exceed the boundaries of the company, creating a real-time relationship with suppliers and customers. For example, the press shop of an automaker will be able to adjust the stamping parameters of a particular coil based on data provided by the supplier. The customer will be able to see the production of his vehicle in real time and he will also be able to propose changes at the last minute. 87% of the automotive industry survey respondents stated that by 2030, the integrated value chain will be closely related. The vast majority of respondents have recognized the benefits of an integrated value chain, which is to reduce costs, increase production flexibility, production quality, and production speed.
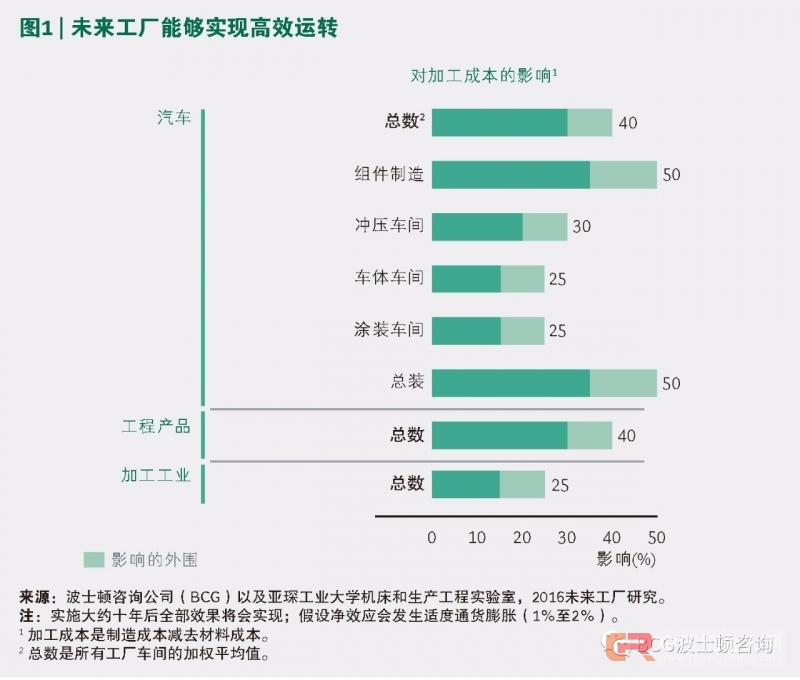
For each factory floor in this integrated value chain, the automotive industry survey respondents gave their opinions on what they considered to be the most important elements in plant structure, plant digitization, and factory processes (see Figure 3).
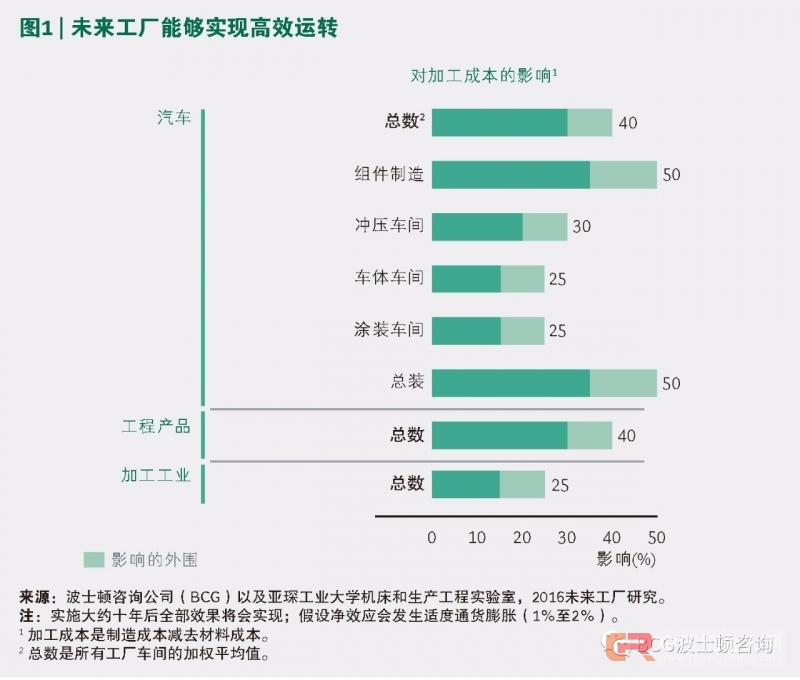
Parts Manufacturing Parts manufacturing will have greater flexibility and better working conditions and will benefit from them. For example, 80% of the automotive industry survey respondents mentioned the relevance of decentralized production guidance, with particular reference to the automatic adjustment of future factory machine parameters in 2030. Almost all respondents pointed out the issue of flexibility in the communication between machines and products. In the production of the camshaft, ThyssenKrupp has assigned a data matrix code for each camshaft. The code contains product data. The product machine scans each camshaft code and adjusts its parameters before performing manufacturing tasks. In addition, more than 70% of respondents said that by 2030, additive manufacturing (generally referred to as "3D printing") will be associated with component manufacturing. Among them, the use of additive manufacturing mentioned not only includes the printing of prototypes, but also the printing of various tools and components. Press shop The efficiency of equipment in the press shop will be greatly improved. 93% of automotive industry respondents mentioned the relevance of predictive maintenance in 2030. In fact, most of the respondents have already implemented their first predictive maintenance or are planning to implement it in the next two years. The Schuler Group of Germany has developed a robot that can not only move components along the press line, but also monitor the condition of various components and send signals to the worker's replacement parts in advance. The Fraunhofer IWU is conducting a study to determine how the press can take corrective measures based on the specific characteristics of the raw materials it receives. 85% of respondents believe that by 2030, energy efficiency will be relevant. Skoda Automotive will install press lines that use 15% less energy than conventional systems to recover the energy released during the press. Body shop The automotive companies are adopting new technologies to increase the flexibility of the body shop. More than 80% of the automotive industry survey respondents said that by 2030, intelligent robots and production simulation will be closely related to the body shop. Automakers are already using robots that can communicate with the car body and adjust their behavior accordingly based on the signals received, while simulations can also assist in the planning and configuration of the shop floor layout. Both KUKA and Microsoft have developed an intelligent system for the body shop that manufactures the Jeep Wrangler. They can not only connect all robots, but also monitor the wear of the robot. Magna implemented a simulation program developed by Siemens that facilitates digital planning and can replicate shop floor operations, for example, interactive collaboration of up to six robots. The paint shop will benefit from the various technologies that will improve the quality of energy efficiency and paint work. More than a third of the automotive industry survey respondents stated that by 2030 energy efficiency will be relevant in the paint shop. For example, in Porsche's factory in Leipzig, Porsche has now used waste heat from nearby biomass power plants to provide carbon neutral supply to meet 80% of the heat requirements in the paint shop. Nearly three-quarters of automotive industry survey respondents said that big data and analytical methods will also be relevant. Most car companies have begun to use big data in the paint shop. Its purpose is to analyze the data to determine the various factors that lead to differences in the paint job and to improve the quality.
The final assembly layout will be more flexible and more versatile, and the final assembly will be the biggest beneficiary. In order to meet the ever-increasing expectations of customers and comply with increasingly stringent government regulations, auto companies will have to introduce more and more types of vehicles; multi-directional layout will lead to more types of production while maintaining high The output of the output. More than 90% of the automotive industry survey respondents expect that by 2030, modular production line settings will be relevant in terms of final assembly. Among them, the flexible and economical replacement of production line components is considered to be particularly important. For example, Toyota is introducing a smaller, more flexible production line, which in turn reduces capital investment in the production line. 85% of the respondents mentioned the relevance of intelligent robots in final assembly. Companies all hope that robotics can make progress, so that each device can perform tasks with high precision requirements. More than 75% of respondents stated that digital factory logistics will be relevant. For example, digital factory logistics can be used to automate replenishment of pre-assembled parts needed for the station. As for the factory process, by 2030, the lean principle will have great significance in the entire value chain. Two-thirds of the automotive industry survey respondents expect that new technologies will enhance the lean management and continuous improvement of production processes. For example, the use of production simulations will enable manufacturers to increase production efficiency, thereby reducing waiting times and working hours. Augmented reality (such as smart glasses) will be able to display operating procedures to assist operators in their assembly and maintenance operations. By using advanced big data algorithms to analyze production data, manufacturers will better understand the overall situation of each production step and continue to improve the production process. Only 7% of automotive industry survey respondents anticipate new technologies that will make lean management obsolete. Three Drivers To realize the vision of a future factory, automakers must address issues related to the three drivers: strategy and leadership, employee skills, and information technology infrastructure. The company must use the future factory strategy as an integral part of the company's strategy and change its leadership style in accordance with the new practice. Manufacturers must also focus on building a team of employees with new skills in order to successfully complete technology-centered production tasks. Finally, companies must establish a complete information technology infrastructure to support the connectivity of the entire value chain while ensuring data security. Strategy and Leadership Manufacturers must incorporate future factory implementation strategies into their overall corporate strategy and build an organizational structure that promotes rigorous management. Of the respondents in the automotive industry, 35% believe that these issues are major organizational challenges. Companies must meet three organizational needs: strategy and roadmap. The future implementation strategy of the factory must be rooted in the corporate strategy. About one-third of respondents in the automotive industry believe that there are major challenges in the future factory strategy. Many companies lack a strategic vision to guide the structured implementation process. management. In order to realize their vision, manufacturers must build organizational structures (such as clarifying future factory guidance and coordination responsibilities) and determine the processes needed to translate future factory strategies into implementation actions. About one-third of respondents in the automotive industry believe that management is a major challenge. The main problems are the lack of communication between departments, the unclear division of responsibilities and the lack of management. New leadership style. Respondents in the automotive industry believe that the consultative leadership style is more important for future factories than the autocratic style. Leadership in transition and group orientation will also receive attention. Employee skills Although the use of robots and computers will reduce the number of jobs in assembly and production, the number of manufacturing jobs that require information technology and data science skills will increase. About 50% of respondents in the automotive industry said they wanted to hire more IT staff, and about 25% expected that the number of IT staff would increase by more than 10% (see Figure 4). About one-third of those surveyed said they needed employees with maintenance and quality control skills, while about 25% said they needed production planning and logistics talent. These additional human resources will provide strong support for the use of new data treasures.
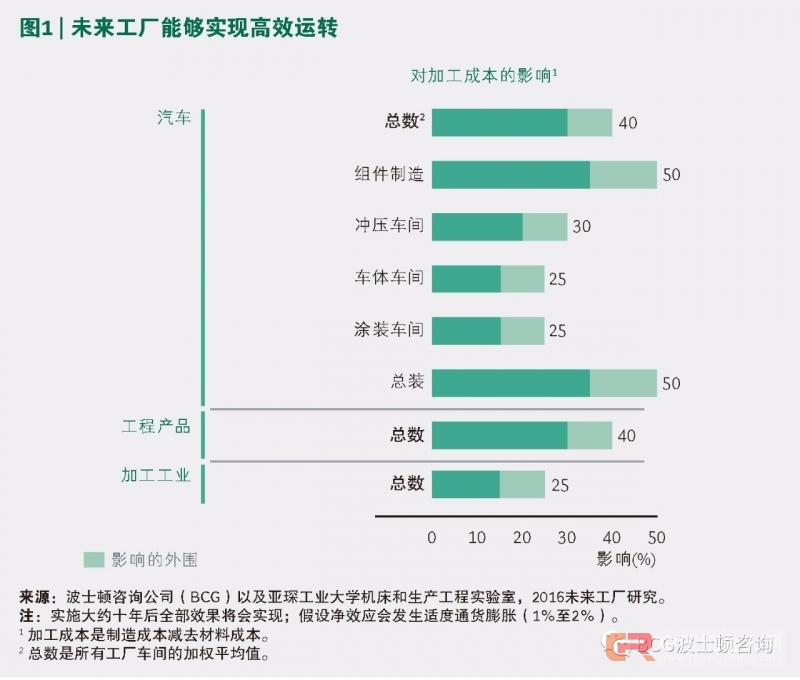
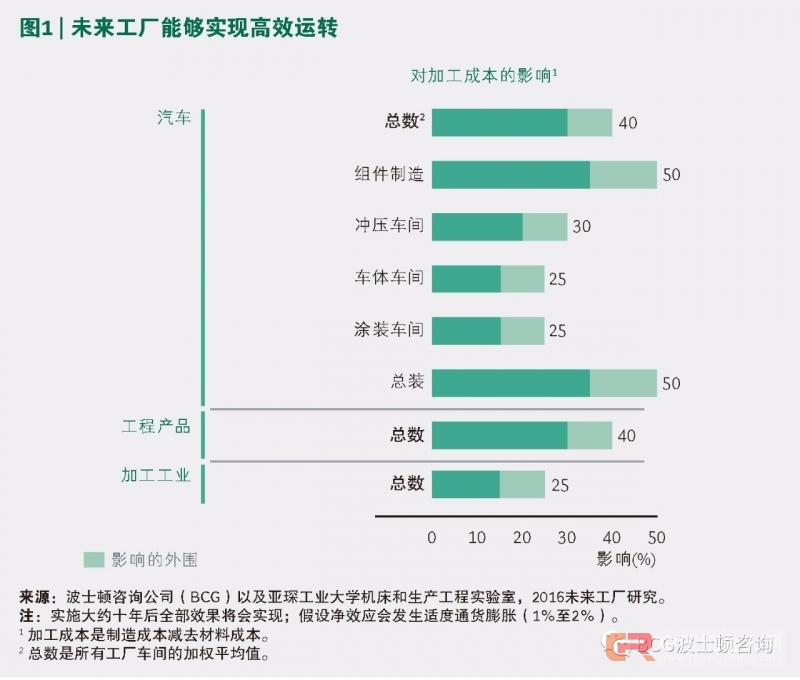
technical skills. Manufacturers need to focus on their technical capabilities and background when training or hiring employees. Respondents in the automotive industry believe that by 2030, skills in information technology, electronics, and “mechatronics” (integrated skills in mechanics, electronics, and information technology) will become more important, and purely mechanical skills will not be favored. Social skills. The future of the factory is very fast, so employees must be willing and able to continuously learn new skills. They are no longer performing repetitive assignments, but are involved as part of interdisciplinary teams to solve problems. More than 90% of respondents in the automotive industry believe that by 2030, the four social capabilities of learning ability, teamwork, ability to take responsibility and solve problems will all become more important. Training and qualifications. Manufacturers cannot expect employees to have the necessary technical and social skills. For a successful transition to a future factory, manufacturers need to develop employee training and assessment methods. In our survey, the majority of respondents in the automotive industry (53%) viewed strengthening employee training as the primary means of providing the required skills. Fewer respondents choose to recruit new employees (29%) or re-educate (18%). Technical learning. The new generation of employees hopes that training can be more flexible and provide more time and space choices. Compared with sitting in a classroom to watch slides, self-study through mobile devices has become the preferred training method. Respondents in the automotive industry seem to recognize the need for innovative and technological learning approaches. They believe that by 2030, real training from practice, online learning and use of virtual environments will become more important; traditional training courses are no longer popular. One-third of IT industry survey respondents believe that IT infrastructure is a major challenge. The following two related requirements must be met: Cloud technology and connectivity. Manufacturers need infrastructure-wide connectivity (for example, wireless LAN) and technology to collect production data and store it. Survey respondents stated that it will be increasingly important to use private cloud services as a central platform for data storage and use software as a service, but they are skeptical about the use of private cloud services. The two main challenges to improving plant-wide connectivity are: lack of network standards and poor network infrastructure. Data Security. Stronger supply chain connectivity is crucial, but protection measures need to be taken to ensure the security of data exchange. Data security is indeed a major concern for car companies. More than 40% of automotive industry survey respondents view data security as a major challenge, and approximately 30% have expressed concerns about data ownership uncertainty. The Boston Consulting Group (BCG) set out to use the results of this study to develop a roadmap for the implementation of future factories (see Figure 6). Each manufacturer must develop a road map based on their respective starting points. In most cases, manufacturers should focus on plant digitization in the short to medium term to avoid lagging behind competitors who are already implementing digital use cases. In the medium and long-term period, the change of the factory structure should be pursued because the change of the factory structure has an impact on all equipment and plant layout. At the same time as changing the structure of the plant, the factory will be generally overhauled or new products will be introduced. For factory processes, manufacturers should continue to adopt new technologies, improve processes, and increase customer satisfaction as an extension of manufacturers' current lean management agenda. Manufacturers should also immediately carry out related work, so that the basic enabling factors as soon as possible, because the training of existing employees, the recruitment of new employees, and the installation of IT infrastructure and other work are very time consuming.
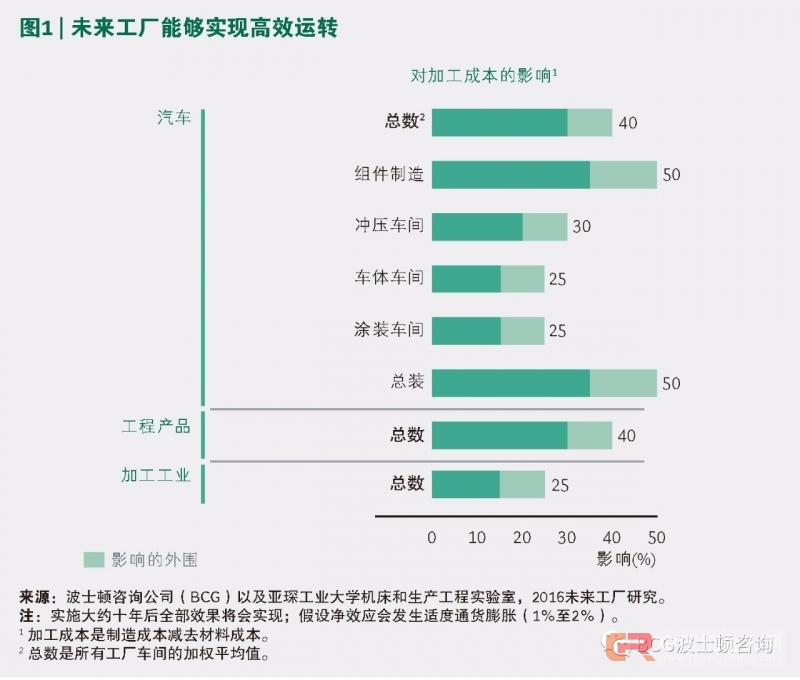
To help manufacturers tailor the implementation roadmap, Boston Consulting Group has developed a "health check" that can quickly assess the status of a company's implementation. Then use the assessment results as a benchmark to compare with other factories, industry averages, or peer groups to determine the starting point of the company. To understand what should be done in the health inspection process, corporate executives and employees can attend advanced technology seminars and presentations held at the Model Factory operated by the Boston Consulting Firm (BCG) Innovation Operations Center (ICO). In order to determine the use cases for inspections, companies can use filters in the BCG database. There are more than 200 examples of future factory applications in the BCG database. Examples are classified according to industry-specific applicability, plant dimensions, or factory floor. Then, experts from the Innovation Operations Center will discuss the use of the use case in detail with a company's factory team, and evaluate the potential technology supplier list to determine the corresponding opportunities, evaluate the expected financial benefits and non-financial benefits, and implement relevant The cost and required investment are quantified. As many of the examples in this report illustrate, manufacturers have begun to approach our future factory vision. But achieving this vision requires more than just fragmented implementation of various use cases. Through the integrated application of new design principles and digital technologies, major manufacturers can intelligently coordinate all aspects of their plant operations while achieving the integration of this value chain from supplier to end customer. The first manufacturers to successfully transition to the large-scale adoption stage will lead the new era of industrial operations.
LED High Bay Light,150W LED High Bay Light,LED High Bay Light with UFO Style
Bailina Lighting Electric Appliance Co., Ltd. , http://www.cn-leds.com
没有评论:
发表评论