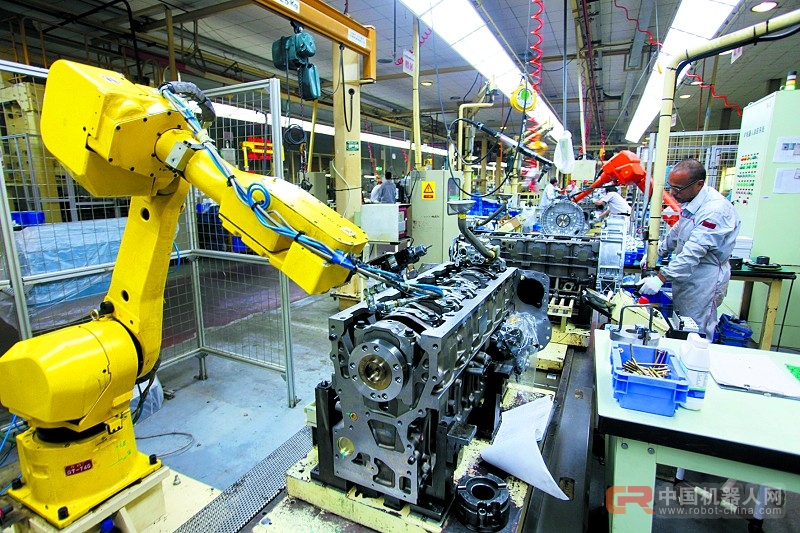
“In the wake of the wave of Industry 4.0, workers should not and cannot be replaced by robots,” said Ding Li, a researcher at the Guangdong Academy of Social Sciences. “There is always a need for people to do the work” The Spring Festival is approaching. Workers working in the city are faced with a problem: Will they return to the original factory to work when they return home for the rest of the year? This is also a concern for factory owners. In the Pearl River Delta region, many factories lose about 10% of their workers each year after the Spring Festival. Some factories even have more. In the case of a bad economic environment, many young people in the 80s and 90s later like to earn higher income through “stirring the way”. However, in the Flextronics Zhuhai Industrial Park, the reporter encountered two post-80s workers who insisted on staying at the original factory—Wang Jian from Hubei and Wang Juan from Hunan. The situation of their factory, Flextronics, is much better than the small and medium-sized factories in the Pearl River Delta region. In more than a decade, more than 90% of the older employees remain in the factory. However, they also faced a new situation - the machine substitution. Since 2006, when “Southwards” entered the factory, Wang Jian had gone from a general operator and a forklift driver on the assembly line to a foreman, a senior foreman, and even a workshop supervisor. He was able to see the “wind and rain” of Flextronics. In the past two years, he has faced a large group of industrial robots called "production revolutions" by workers. In the Pearl River Delta where the manufacturing industry is densely populated, factory owners choose “machine substitution”. The purpose is twofold: first, the loss of hectic workers and the “difficulty of recruiting workers”; secondly, they want to increase production efficiency and quality in order to save costs. The deeper reason lies in the fact that under the background of sluggish international and domestic economies, manufacturing companies represented by processing trade enterprises are facing rising costs, sharply fluctuating international orders and harsh market conditions. Although the problem of staff turnover is not serious, Flextronics is also facing the problems of “cost” and “market”. According to Valerie, Head of Asia Marketing for Flextronics, in the face of market pressure, Flextronics is preparing to remove the “world’s second largest foundry” hat and reposition itself as a “solution provider” that spans product concept formation to mass production. In order to "retain" customers with more value-added services and value-added services, and open up new markets. The shift in positioning means that Flextronics is no longer simply picking up assembly production as it used to, but also cutting into the entire product life cycle of product development, design, market development, distribution logistics, and instant tracking. To complete this "transformation", the factory needs at least two major helpers - industrial robots and industrial networking. While industrial robots “enhance quality and increase efficiency”, industrial big data will be imported into the unified “industrial cloud” platform through the Internet of Things, and big data will become the basis for decision-making on the optimization of production efficiency and product R&D. It is understood that Flextronics is promoting the application of "wink", an industrial control system developed independently, in its factories. While purchasing imported industrial robots in large quantities, Flextronics engineers developed an operating system for robots to adapt to their production. Undoubtedly, the transition of Flextronics is a microcosm of the progress made by many manufacturing enterprises in the Pearl River Delta region to the “smart factory”. However, industrial robots have come. What about ordinary workers? "Flextronic does not consider moving from Zhuhai because the factory needs the Pearl River Delta's industrial chain and workers in Zhuhai." Valerie first gave the reporter a "centering pill." "The factory needs robots to complete the production transformation, but workers are also indispensable." Resources. Regardless of the extent to which industrial robots are used, there is always work that needs to be done.” Her understanding of Industry 4.0 is that robotic applications must first replace people for simple, repetitive and dangerous work, and people do more of their work. work. It is understood that Flextronics has expanded to the production of new medical devices based on the original consumer electronics products. The new industry is enough to accommodate the transfer of workers. Another more advanced "transfer job" is when some workers are trained to become robotic engineers. Mao Xiaolong, the Flextronics Zhuhai factory automation manager, said that robots are like brothers who started work with workers. The introduction of robots brings "upgrades" to the work, giving workers more dignified work. In the Flextronics Zhuhai factory, simple or highly demanding jobs such as handling and processing of spare parts have been replaced by industrial robots. Many workers changed jobs to engage in more complicated product assembly and packaging. In the workshop, the robot arm constantly flaps, and the scene where the workers “assisted” the handling of spare parts can be seen everywhere. To meet the vision of workers' growth Ding Li, a researcher at the Guangdong Academy of Social Sciences Research Institute, has long been concerned about the industrial transformation of Guangdong and has investigated the "smart factories" of Germany and Japan. He said that the concept of Industry 4.0 is by no means a simple replacement for human labor, but emphasizes the protection of people. The work that can be done by robots and humans must first be open to people; only when the efficiency of robots exceeds that of humans in large scale, can robots be considered. But there is only work. It is not the only vision of "new generation" workers after the 80s and 90s. “Our generation is not the same as our father’s generation. Parents work as long as they need money, and we want to live a dignified life in addition to money. We also need to see hope for growth.” Wang Juan’s thoughts, and many migrant workers of the same age Coincide. Whether or not there is a "crowd-out effect" of machine substitution, some young people choose to leave the factory to seek better treatment and a better environment for development. This is also a big background for many manufacturing companies in the Pearl River Delta region facing the problem of “recruitment difficulties”. In response, some of the more foreseeing companies have proposed their solutions—the space for workers to grow. “In the Pearl River Delta region, some young workers resigned their jobs and changed jobs. After working for five or six years, they were still a general worker. Don't you find it strange?” said Ho Chu Hor, another marketing executive at Flextronics. Asked reporters, "The best situation is that a worker gradually deepens in the same field and achieves promotion of positions and salaries." Ho Chu Hor emphasized that manufacturing companies need to pay enough attention to employee benefits in order to maximize the value of employees. In order to promote the growth of corporate performance. Wang Jian is the leader in "upgrading" employees. After going through multiple jobs, Wang Jian determined to learn new knowledge to deal with factory management in the Industrial 4.0 era. However, this high school graduate needs to "self-taught," and it is difficult to imagine. Wang Jian told reporters that his basic subjects such as mathematics and English are not good, and he can only use the evening and weekends to study on his own. Fortunately, several of his superiors have read MBAs and often answer questions for him. With the help of factories and colleagues, Wang Jian obtained a bachelor's degree from Beijing University of International Business and Economics through continuing education. He believes that there is a school atmosphere in the factory, which is a key to his growth. In addition, in the Flextronics campus, there are all kinds of facilities: sports fields, fitness rooms, counseling rooms, dormitories, and so on. At the same time, we will consider issues such as blind date and settlement of employees. This is another key to the factory's retention of employees. It was exactly a year ago that Wang Jian met his current wife. The two parties met each other during the friendship activities in different departments and finalized the marriage after six months. Coincidentally, Wang Juan also met the current husband in the factory. The two have already purchased their houses near the factory and settled in Zhuhai. They then took home with their parents. As Wang Juan settled down in the area, Wang Jian “highly promoted” and therefore they did not want to leave the factory; and because the old staff were rooted locally, the factory should not be removed. From the point of view of the development of Flextronics, both factories and employees have achieved a benign “bundle”. For manufacturing workers in the Pearl River Delta, they have a stable life and work and can continue to grow on this road. Their transformation has become increasingly clear.
Fiberglass fabrics are used in a wide range of industrial applications and are the most widely available and least expensive composite fabric. It is relatively lightweight, has moderate tensile and compressive strength, and is easy to handle and machine. High strength, dimensional stability, design flexibility and excellent electrical properties are some of the characteristics that insure optimum performance.
There are several types of glass fibers manufactured but only two are widely used in composites: E-glass and S-glass. The most common is E-Glass or Electrical Glass. E-Glass is made from strands of continuous glass filaments that are plied and twisted into yarns and is used when strength and high electrical resistivity is required. S-Glass or Structural glass is approximately 30% stronger and stiffer than E-Glass and offers better properties at elevated temperature.
Our Woven Fiberglass Cloth Fabric Specialty
high temperature proof fiberglass fabric like 3732 and 7628,HT800
It has: plain weave, twill weave, satin weave, gauze weave.
a). Plain weave: it can be used in electricity insulation materials and reinforced materials in industry, because of inseparable structure, plain and clear lines. Such as EW140, EW7628. 3732,
b). Twill weave: compared with plain weave, it is of high density, high intensity, with a soft and loose structural weave. It can be used in ordinary reinforced materials, filter materials, and painting cloth, such as EW3732, EW3784.
c) Satin weave: compared with plain weave and twill weave, it is of high density,high intensity, with a soft and loose structural weave with a good texture. It is applicable for use as a higher reinforced material in machinery, such as EW3784,EW3788.
d). Gauze weave: said lattice twist weave. It can be used in spread model curtain,resin reinforced emery wheel gray cloth and lattice embed belt. specification:5*5, 6*6 and 8*8
Fiberglass Cloth,Fiberglass Cloth Fabric,Woven Fiberglass Cloth
JinYuan Group-NingBo JinYuan Insulation Material Co.,Ltd , http://www.ccl-manufacturer.com
没有评论:
发表评论