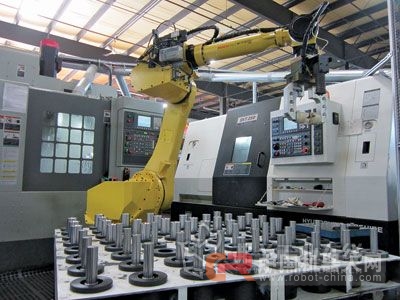
What people are worried about is that the “encumbered economy” brought about by excessive policy guidance, overcapacity brought about by over-investment by industry, and low-end homogenous competition brought about by lack of innovation drive will bring the robot industry into Disorderly development. It is worth considering that what kind of company is best suited for developing industrial robots? How to improve the overall quality of the robot industry? In general, companies that have the foundation of numerical control systems, control systems, servo motors, and servo control systems that can mass produce have certain advantages. The FUNAC company’s industrial advancement route is a typical case of success and is worth learning from. Several domestic CNC system companies have entered the industrial robot industry one after another, taking the lead in Guangzhou CNC. Since 2006, the industrial robot industry has been planned and developed for eight years. With the experience accumulated in the production of its own controllers, servo drives and servo motors, it has completed its own independent development of serialization of industrial robots. The products cover 3 to 200 kg. Functions include handling, machine loading and unloading, welding, palletizing, and gluing. Polishing, cutting, painting, sorting, assembly, etc. With the rise of labor costs, lack of skilled personnel, high-risk environmental protection, high-intensity operations and other issues highlighted, industrial robots have been widely recognized and continuously used in manufacturing, and have become the focus of social concern. The government is also using this to promote industrial transformation and upgrading. Enterprises use it to carry out technological transformation, change production methods, and improve operational efficiency. However, China’s robot ownership is not large, national brands are still under cultivation, and the overall competitiveness needs to be improved. So, what kind of model will the robot industry develop? At this stage, the collaborative development of the entire industrial chain of robot companies, robot key component suppliers, and robot integrators is needed. The integration of robots and CNC machine tools In the field of numerically-controlled machine tool processing applications, the integration of local machine tool loading and unloading robots and CNC machine tools has been developed at the forefront. From the industrial application level, there have also been major changes: (1) Work Island: single-to-single-unit motivation plus single-to-many online processing. (2) Flexible Manufacturing System (FMS): Based on the network-controlled flexible machine line addition, the PLC control platform is adopted, and multiple robots, multiple CNC machine tools and their auxiliary equipments are connected to the group cable by means of an industrial Ethernet bus. Beats for orderly automatic production. (3) Digital workshop: With CAD\CAM\CAPPS\MES auxiliary production tools, logistics technology and sensor technology, with production process monitoring, real-time feedback of online faults, processing process data management, tool information management, equipment maintenance data management, products Information recording and other functions to meet the needs of unmanned processing, to achieve the production system of the production system, job coordination, integration and optimization of operation. (4) Smart factory: With the help of intelligent workshop layout and ERP information management system, it will bring innovation to traditional production methods to the maximum. The database of the information management system can be interfaced with various external information systems through the gateway, and the workshop can be connected to the ERP system to query the production status of the workshop to realize the efficient configuration of the enterprise resources. With the help of its short message platform and mail platform, it can be conducted to the administrator. Real-time reporting of equipment failures, production schedules, and other information. Industrial robots and CNC machine tools integration development approach 1. Processing and manufacturing: the robot involved in machine tool structure parts manufacturing to achieve automation, special machine tools to serve the robot special reducer precision machining, improve the quality of processing technology and mass production efficiency, etc. Great integration of development space. With the strategic cooperation of both companies, robotics companies can use the manufacturing and process capabilities of machine tool manufacturers to achieve the following goals: (1) Body-casting and speed reducer structural parts for robots, jointly researching the formation of batch precision manufacturing technologies, and improving the mass production of robots Ability and craftsmanship level to overcome reliability, consistency technology, and achieve efficient, stable and precise beat production. (2) For robot tooling, fixtures, machine-integrated production line integration capabilities, with the help of the vast end-customer channel resources of major machine tool plants, commissioned to promote the use of robots. (3) Research and development of industrial robots that are needed for automatic and flexible production of machine tools and production lines for cutting and parts handling, scraping, chamfering, polishing, welding, and spraying (powder), etc. Machine tools companies and industrial robot companies jointly develop , to achieve the automatic processing of the whole machine parts, and promote the improvement of the machine tool manufacturing technology level. (4) Key components of industrial robots, such as rotary disks, booms, boxes, support sleeves, small arms, wrists, etc., are required to have high dimensional accuracy and form-position tolerance. They are used for mechanical processing equipment and fixtures. There are high requirements for quantity inspection tools; structural optimization and processing of key components such as cycloidal gear case, planetary pin wheel, eccentric shaft and planet carrier of the robot reducer, the current domestic processing equipment, assembly process, precision detection, etc. Still difficult to reach. However, based on the use of domestic CNC machine tools and tools to complete the relevant processing, it will help improve China's high-end precision machinery parts design and processing level, and promote the application of domestic CNC equipment and domestic CNC machine tools and development. 2. In the aspect of integrated application: Machine tool loading and unloading robots to achieve machine plus flexible production line will be a convenient and effective promotion method. The number of domestic CNC machine tools is approximately 2 million units. The robot companies' first application of the machine tool loading and unloading flexible machine plus production line will have a great market demand, and it will also help facilitate the automation and digitization of machine components such as machine tools and robots. The networked production method can realize process intelligent control and information management, can increase production efficiency and product quality, and improve the level of process management until the overall level of equipment manufacturing industry is promoted. For example, Guangzhou CNC has formed strategic partnerships with machine tool manufacturers such as Dalian Machine Tool and Baoji Machine Tool Co., Ltd. to jointly develop robot-specific processing machine tools, processing technology applications, and robotic robots with automatic flexible production and application projects, which have promoted the mutual integration of the two parties into their respective industrial applications. There is a gap between the domestic robots and machine tool industry and the international advanced level, especially as an industrial robot in emerging industries, which started later than the domestic machine tool industry, regardless of the manufacturing process level, control system, or integrated application experience; regardless of the maturity of the technical standards, or professional personnel The degree of ownership has all constrained the current pace of development. It is still necessary to seek progress in exploration. However, we believe that the deep integration of the two is of great significance for improving the overall competitiveness of China's equipment manufacturing industry.
Antenk D-Sub,D-Shaped Connectors Solutions offer a broad range of higher reliability D-Sub connectors.
Antenk's D-Sub product line is designed for applications that require a rugged, robust I/O connector system with various styles and mounting options. All are used in a variety of industries including computer, industrial, medical, and military markets.
Antenk High-Density D-Sub Connectors
Available in cable mount options including crimp & solder cup and the board mount options including Dip Solder, Wire Wrap, High Profile, Right Angle, & Surface Mount (SMT). This comprehensive Antenk High-Density Density D-Sub product offering is available in both stamped & formed and machined contact options.
High density D-Sub connectors, for applications where the best possible contact density is required. Due to the [high" density of the 15, 26, 44, 62 and 78 contacts, this series is ideal for the most modern applications. The insulating body, a monoblock, complies with the UL94 V-0 standard. The contacts are machined and available in several quality classes.
Antenk Solder Type D-Sub Connector
Available in standard and high density versions
Supplied with stamped & formed or screw machine contacts.
Standard contact terminations accomodate up to 20 AWG standard wire
Available with white (nylon) or black (PBT) insulators. Standard shell plating is tin
Antenk D-Sub connectors solder cup machined contacts are manufactured according to the standards MIL-C-24308 and DIN 41652. The standard connectors from Antenk are available in all known versions and sizes. They are available in various version with numerous assemblies. The insulating body, a monoblock, complies with the UL94 V-0 standard. The contacts are machined and available in several quality classes.
Features of Antenk's Solder Cup Standard D-Sub Connector Machined contacts
Solder cup d-sub available in 5 industry sizes/positions
Standard Density ( 9 pin , 15 pin , 25 pin , 37 pin , 50 pin)
Tin shells have indents to provide grounding and additional retention.
Screw machine contacts offer high reliability. Non-removable contacts.
Optional mounting hardware available.
Materials of Antenk Solder Cup Standard D-Sub Connector Machined contacts
Shell: Steel, tin plated
Insulator: Glass-filled thermoplastic. U.L. rated 94V-O
(260°C process temp)
Machined contacts:
Male pins - Brass | Female pins - Brass
Plating: Gold flash on entire contact
Contact us for other plating options
Features of Solder Cup High Density D-Sub Machined Contacts
Solder cup d-subs in 4 industry sizes/positions
High Density (15 pin, 26 pin, 44 pin, 62 pin).
Approximately 65% more higher density then standard d-sub connectors.
Screw machined contacts offer high reliability.
Metal Shell provides EMI/RFI shielding. Available in 3 clinch-nut options.
Plug shells have indents to provide grounding & additional retention.
Connectors will fit in standard D-Sub Backshells .
Contacts will accept (28 - 24) gauge wire.
Materials of Solder Cup High Density D-Sub Machined Contacts
Shell: Steel, Nickel plated
Insulator: Glass-filled, PBT Thermoplastic. U.L. rated 94V-O
(230°C process temp)
Machined contacts: Brass, Gold Flash Plated(contact us for other plating options)
9 pin, 15 pin, 25 pin, 37 pin, 50 pin Male Solder Cup Standard D-Sub Connectors Machined Contacts, Solder Cup High Density D-Sub Machined Contacts,Female Solder Cup Standard D-Sub Connectors Machined Contacts
ShenZhen Antenk Electronics Co,Ltd , https://www.antenk.com
没有评论:
发表评论